Quando serve il Perito Navale: Perizie imbarcazioni usate e nuove. Perizie legali, di parte. Perizie assicurazioni Perizie per polizza Corpi, Perizie valutative, leasing. Osmosi, delaminazioni, sinistri marini.
Il Perito nautico al vostro servizio. Perizie navali commerciali. Ispezioni con Ultrasuoni e Termografia.
La costruzione a sandwich è da considerarsi “l’uovo di Colombo” quando si vuole ottenere una struttura leggera ed estremamente rigida.
Per capire meglio immaginiamo cosa avviene negli stratificati semplici sottoposti a flessione: una delle parti esterne è sollecitata a compressione mentre l’altra a trazione, invece al centro, nell’asse neutro, la sollecitazione è nulla.
Quindi la parte del materiale strutturale prossima all’asse neutro del laminato non viene sfruttata al massimo delle sue potenzialità perché non sollecitata.
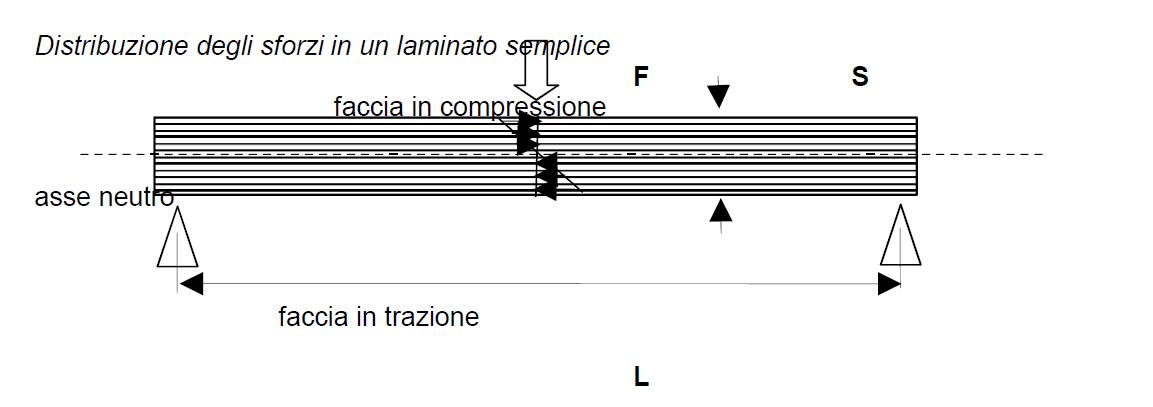
Invece nella struttura a sandwich il materiale che deve essere sollecitato viene posto distante dall’asse neutro di flessione, con i vantaggi di sfruttarlo integralmente aumentandone il momento di inerzia. Nella struttura a sandwich la distribuzione degli sforzi ai vari livelli del laminato è lineare.
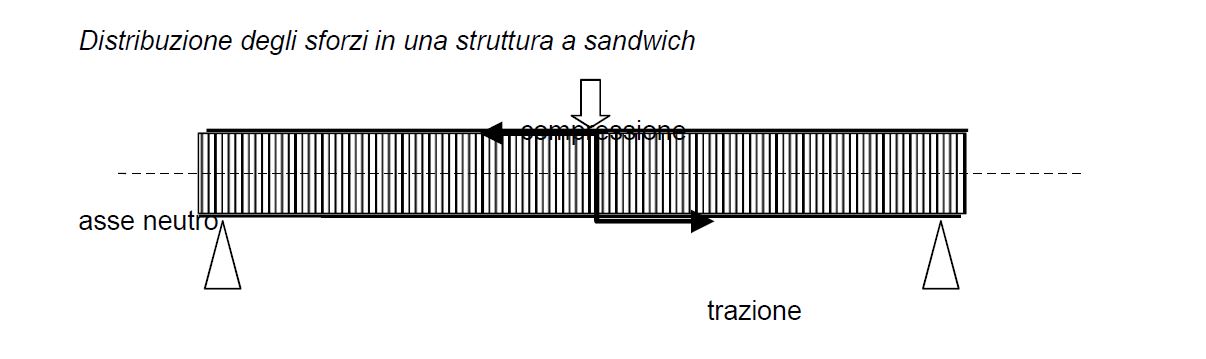
Il sandwich è composto da un’anima in materiale leggero e incomprimibile, con le due facce ricoperte da un laminato inestensibile chiamato la pelle.
Sottoponendo questa struttura a flessione, una delle pelli viene sollecitata a trazione e l’altra a compressione.
Dal momento che le pelli sono costituite da materiali con elevato modulo di Young, come uno stratificato, oppongono una elevata resistenza a queste sollecitazioni, comportandosi come materiali inestensibili e incomprimibili.
Fermo restando questo concetto, nella deformazione della struttura le pelli sono costrette ad avvicinarsi, quindi a ridurre lo spazio che le separa, perché tendono a descrivere lo stesso arco.
Se le pelli sono distanziate da un materiale che non si comprime, il gioco è fatto: si ottiene una struttura con una rigidità di gran lunga superiore a quella di un laminato di spessore pari alla somma delle due pelli del sandwich.
Alla stregua di ciò, la struttura a sandwich consente di ridurre gli spessori delle pelli pur mantenendo un’elevata rigidità.
L’altro elemento determinante della struttura a sandwich è lo spessore dell’anima: maggiore è la distanza tra le pelli più alto è il momento di inerzia.
Nel progettare una struttura bisogna tener conto di questo fattore e trovare ll giusto compromesso tra lo spessore delle pelli e lo spessore dell’anima, tenendo conto anche della sua resistenza alla compressione.
In genere nei materiali utilizzati come anima, specialmente negli espansi, la resistenza alla compressione viene determinata dalla densità: un’alta densità corrisponde ad una maggior resistenza alla compressione.
In teoria un’anima di spessore elevato dà luogo ad una struttura più rigida; quindi si può ricorrere anche ad un materiale a bassa densità; inoltre, se il pezzo non dovrà sopportare forti sollecitazioni, si può ridurre anche lo spessore delle pelli senza perdere in rigidità.
Man mano che si riduce la distanza tra le pelli, bisogna impiegare un’anima di densità più elevata, perchè sottoposta a flessione, l’anima risulta progressivamente più sollecitata a compressione.
Nelle costruzioni a sandwich, le pelli sono in genere in stratificato, con fibre di vetro, di carbonio o di Kevlar. In alcuni pannelli si utilizza l’alluminio, oppure, per motivi estetici, uno stratificato con la finitura in legno. L’anima può essere in diversi materiali a seconda dell’impiego, purché dotati dei requisiti di leggerezza e resistenza alla compressione.
L’anima per eccellenza è quella con struttura alveolare a nido d’ape.
In ordine di prestazioni vi è quella in alluminio, utilizzata in prevalenza nel settore aeronautico.
Un altro materiale molto diffuso è In Nomex (carta in fibra aramidica impregnata con resina fenolica.) utilizzato negli impieghi di alta tecnologia.
Per lavori dove il fattore preso non è determinante si utilizzana il nido d’ape in polipropilene o in policarbonato.
Le celle sono di forma esagonale, disponibili in varie dimensione, da 3 a 8 mm. che ne determinano la densità. Quelle in alluminio e in Nomex vengono anche prodotte con la cella rettangolare (esagono allungato) per migliorarne l’adattabilità nelle parti con forte curvatura. Gli spessori delle lastre di uso corrente vanno da un minimo di 3 mm a 30 – 40 mm. Quelle in Npmex sono disponibili anche con spessori molto alti in quanto possono essere tagliate nello spessore per ottenere ad esempio un profilo alare.
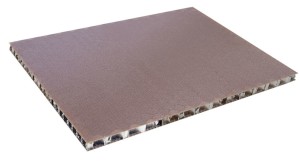
Nele costruzioni con il nido d’ape si utilizzano quasi esclusivamente fibre preimpregnate, le quali devono polimerizzare a caldo in autoclave. Non si può impregnare il tessuto direttamente sul nido d’ape altrimenti le celle si riempiono di resina. L’unica alternativa in questo caso è impregnare il tessuto su un foglio di Mylar e poi adagiarlo sul nido d’ape e pressare sotto vuoto. Questo tipo di costruzione richiede molta esperienza e viene realizzato da aziende specializzate, con l’ausilio di attrezzature adeguate.
La condizione essenziale in una struttura a sandwich è la perfetta aderenza delle pelli all’anima. E’ sufficiente una piccola zona con scarsa aderenza, che si propaga con le sollecitazioni, per provocare il cedimento di tutta la struttura. Questo avviene in genere nella parte sollecitata a compressione, dove la pelle, per scarsa aderenza tende ad accartocciarsi.
La struttura a nido d’ape presenta un’area di incollaggio effettiva molto esigua, dato il sottile spessore delle pareti delle celle. In compenso le resine, per effetto della capillarità hanno la tendenza a bagnare una piccola quota della parete della cella, aumentando la superficie di aggancio. Per avere un’idea sulle avvertenze necessarie nell’utilizzo di questi materiali, ad esempio vi è l’accorgimento di non maneggiare i fogli del nido d’ape con le mani nude, bisogna indossare guanti in cotone per non contaminali con il grasso delle mani, che potrebbe compromettere l’adesione.
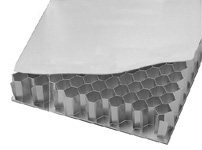
Il nido d’ape in polipropilene viene fornito con le due facce già ricoperte da un non tessuto termosaldato. Questo serve ad assicurare l’aderenza delle pelli al polipropilene che altrimenti sarebbe scarsa. Con questo tipo si eseguono in genere pannelli con le pelli in vetroresina prefabbricate e incollate; l’adesivo, a base di resina, impregna il nontessuto che determina l’aderenza. In genere il nido d’ape in polipropilene viene impiegato nella
costruzione di pannelli in edilizia In tutti gli altri settori, specialmente in quello nautico, si utilizzano anime in materiale espanso.
La costruzione del sandwich risulta più semplice e non occorrono le particolari attrezzature come per il nido d’ape. Si possono stratificare le pelli direttamente sul pannello di espanso; se si dispone di un impianto per il vuoto, si può completare la stampata del sandwich in una sola operazione. L’adesione delle pelli sulla superficie dell’espanso è ottima, grazie agli alveoli, che presentano uno sviluppo di superficie effettiva, maggiore dell’area del pannello.
Da diversi anni, i materiali espansi hanno avuto un notevole incremento nel settore nautico, perché consentono drastiche riduzioni del peso. Inoltre offrono la possibilità di costruire imbarcazioni con il sistema one off, senza la necessità di uno stampo, come vedremo più avanti.
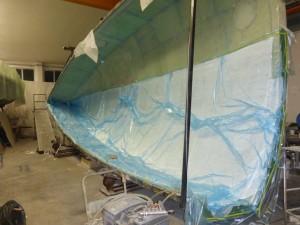
I materiali espansi utilizzati come anima sono polimeri; il più diffuso è il PVC espanso, meglio conosciuto con il nome “Termanto”.
E’ un espanso rigido a cellula chiusa fornito in lastre, disponibile in diversi spessori e densità. Un’altro interessante materiale è il Roacel: polimetacrylimide (PMI) più costoso ma con maggior resistenza alla compressione a parità di densità. E’ un materiale molto rigido, poco adattabile alle superfici curve.
Questi materiali resistono bene ai solventi, quindi possono essere stratificati anche con le resine poliesteri e le vinilesteri.
Lo Styrofoam è un polistirolo espanso estruso, a cellula chiusa molto compatta. Ha una struttura completamente diversa dal normale polistirolo espanso che è composta da “pallini” aggregati. Lo Styrofoam ha una cella finissima, quasi invisibile ed è disponibile in un’unica densità di 45 kg./m3. Ha una resistenza alla compressione inferiore a quella del PVC espaso, però offre un’ottimo compromesso tra qualità, peso e prezzo. Lo styrofoam deve essere resinato solo con le epossidiche.
Anche il legno di balsa viene impiegato come anima. Contourkore sono blocchetti di balsa tagliati perpendicolarmente al senso della vena e riassemblati in pannelli, con la vena di testa per avere la maggior resistenza a compressione. Ha una densità di circa 90 kg/m3, più elevata rispetto alla media degli espansi, però si ottengono manufatti estremamente resistenti, grazie all’ottimo connubio con le resine, che riescono a penetrare nella capillarità del legno, creando un eccellente legame tra le pelli e la struttura dell’anima .
Purtroppo non ha la diffusione che le spetterebbe nel settore nautico, in quanto ha l’inconveniente, con il tempo di assorbire acqua e quindi appesantirsi. Questo può avvenire sia per l’effetto dell’osmosi che attraverso minuscole lesioni, o interventi successivi alla costruzione.
Il PVC espanso, come anche la balsa, vengono forniti in pannelli rigidi, o almeno che consentono curvature ad ampio raggio. Per le forme più complesse o curvature di piccolo raggio, è disponibile il tipo “quadrettato “ screen colth . Trattasi dello stesso materiale rigido, però tagliato in piccoli quadrati di 3 cm, di lato, incollati su una garza in tessuto di vetro che ha lo scopo di tenerli uniti. In questo modo il pannello risulta perfettamente adattabile a qualsiasi superficie.
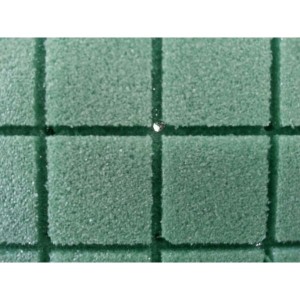
Dal momento che l’anima lavora a compressione, non perde assolutamente nulla in resistenza a causa dei tagli della quadrettatura. Infatti nel disporre il pannello di espanso per creare l’anima, non ha importanza che questo sia intero, può anche esse assemblato con vari pezzi semplicemente accostati, ed ottenere identica resistenza meccanica.
In alternativa al tipo quadrettato, esistono degli espansi cosiddetti “ duttili” che possono essere curvati o addirittura piegati ad angolo retto senza rompersi. Questi sono anche termoformabili: si possono preformare con un fon industriale, e mantengono la forma acquisita. Fino a spessori di 10 mm. questi possono essere arrotolati senza problemi, quindi molto comodi per le spedizioni. Hanno però un costo più elevato rispetto ai tipi rigidi.
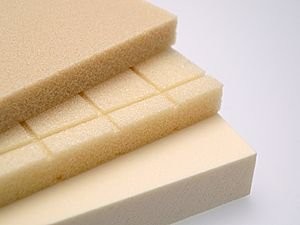